Bridging the Gap: TPO and rCB in the Global Supply Chain for Sustainable Manufacturing
THE STORIES
TYROIL
7/7/20254 min read
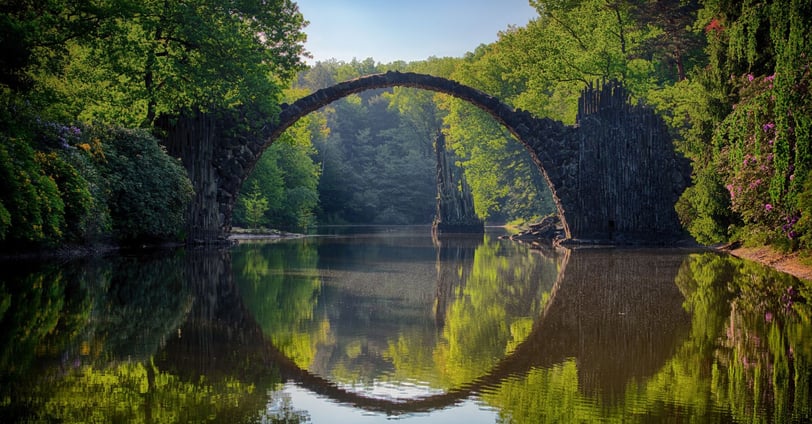
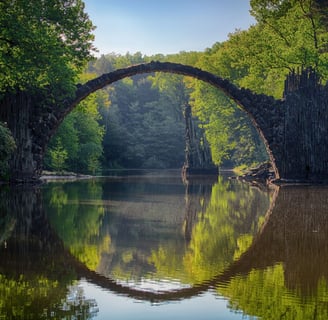
In today’s hyper-connected world, the journey of a product from raw material to consumer is a complex, global dance. But this intricate supply chain, once a symbol of efficiency, is now under intense scrutiny. Consumers, investors, and regulators are increasingly demanding transparency and sustainability, pushing global corporations to rethink every link in their chain. The pressure is on to reduce carbon footprints, embrace circularity, and move away from a reliance on virgin, fossil-based materials. This is where Tire Pyrolysis Oil (TPO) and Recovered Carbon Black (rCB) emerge as critical enablers, bridging the gap between the demand for sustainable manufacturing and the practical need for high-quality, reliable raw materials.
The Green Wave: A Shift in Corporate Consciousness
For decades, the primary focus of global supply chains was cost and efficiency. Now, a third, non-negotiable pillar has been added: sustainability. This shift is driven by several key factors:
Consumer Demand: A growing number of consumers are making purchasing decisions based on a company’s environmental and ethical credentials. They want to know where their products come from and that they are made responsibly.
Investor Pressure: Investors are increasingly using Environmental, Social, and Governance (ESG) criteria to evaluate companies, recognizing that sustainable practices are linked to long-term financial performance and risk mitigation.
Regulatory Requirements: Governments around the world are implementing stricter regulations on waste, emissions, and recycled content, compelling companies to adapt or face penalties.
This “green wave” has sent a clear message to global corporations: sustainability is no longer a niche marketing tactic; it is a core business imperative. The challenge, however, lies in finding sustainable raw materials that meet the rigorous quality and performance standards of modern manufacturing.
TPO as a Sustainable Feedstock: Decarbonizing Manufacturing
Imagine a multinational manufacturing giant, "GlobalChem," that produces a wide range of industrial chemicals and materials. For years, their operations were heavily reliant on fossil-derived feedstocks, contributing significantly to their carbon footprint. Facing pressure from their stakeholders, GlobalChem began searching for sustainable alternatives. Their search led them to TPO.
TPO offers a powerful solution for decarbonizing manufacturing processes:
Alternative to Fossil Fuels: TPO can be used as a direct substitute for conventional fuel oil in industrial boilers, furnaces, and cement kilns. This not only reduces reliance on virgin fossil fuels but also lowers the overall carbon intensity of the manufacturing process, especially when considering the avoided emissions from landfilling tires [1].
Sustainable Chemical Feedstock: TPO is a rich source of valuable chemical compounds, such as aromatics and olefins, which are the building blocks for many plastics, resins, and synthetic fibers. By using TPO as a feedstock, companies can reduce their dependence on petroleum-based chemicals, creating a more circular and sustainable chemical industry [2].
Reducing Scope 3 Emissions: For many corporations, the majority of their carbon footprint lies in their supply chain (Scope 3 emissions). By sourcing TPO from producers who are diverting waste from landfills, companies can significantly reduce these upstream emissions, making substantial progress towards their climate goals.
GlobalChem’s adoption of TPO not only improved its environmental performance but also enhanced its brand reputation and strengthened its relationships with environmentally conscious customers and investors.
rCB as a Circular Material: Closing the Loop
While TPO addresses the energy and chemical side of manufacturing, rCB tackles the material side, offering a prime example of the circular economy in action. Virgin carbon black (vCB) is a critical component in countless products, from tires and automotive parts to plastics, inks, and coatings. However, its production is energy-intensive and relies on fossil fuels. rCB provides a sustainable, high-performance alternative.
Consider a leading automotive manufacturer, "AutoCorp," committed to producing the world’s most sustainable vehicles. They recognized that a significant portion of their environmental impact came from the tires on their cars. By partnering with rCB producers, AutoCorp was able to:
Incorporate Recycled Content: Use rCB in their new tire specifications, significantly increasing the recycled content of their vehicles and reducing their reliance on virgin materials [3].
Lower Embodied Carbon: The use of rCB, with its lower manufacturing footprint compared to vCB, helped AutoCorp reduce the overall embodied carbon of their vehicles, a key metric for sustainability.
Meet Circularity Targets: By creating a demand for rCB, AutoCorp helped to close the loop on tire materials, ensuring that old tires were transformed into new, high-value products, rather than ending up in landfills.
This partnership not only enhanced AutoCorp’s sustainability credentials but also created a more resilient and circular supply chain for a critical raw material.
Global Collaboration: The Indonesia Connection
The beauty of the TPO and rCB story lies in its potential for global collaboration. A multinational corporation headquartered in Europe or North America can partner with TPO and rCB producers in Indonesia, creating a win-win scenario:
For the Corporation: Access to a reliable supply of high-quality, sustainable raw materials, helping them meet their ESG goals and enhance their brand reputation.
For Indonesia: A new market for its TPO and rCB products, driving investment in its green economy, creating jobs, and solving a pressing local waste problem.
This cross-border collaboration is a powerful example of how global supply chains can be a force for good, connecting the demand for sustainable products with the supply of innovative, circular solutions from around the world. It’s about building bridges between nations, industries, and communities, all in the pursuit of a more sustainable future.
Conclusion: TPO and rCB – The Future of Sustainable Manufacturing
The era of unsustainable, linear supply chains is coming to an end. The future of manufacturing belongs to those who can innovate, adapt, and embrace circularity. Tire Pyrolysis Oil and Recovered Carbon Black are not just niche products; they are fundamental building blocks for this new, sustainable paradigm.
By providing high-quality, low-carbon alternatives to fossil-based fuels and materials, TPO and rCB are empowering global corporations to meet the growing demand for sustainable products. They are bridging the gap between ambition and action, turning the vision of a circular economy into a tangible reality. As more companies integrate TPO and rCB into their supply chains, they are not just making better products; they are building a better, more resilient, and more sustainable world for us all.
More Related Articles:
Beyond Compliance: The Future of ESG and Tire Pyrolysis in Corporate Strategy
Community & Conscience: The Social Impact of Tire Pyrolysis on Corporations
The Invisible Shield: How Pyrolysis Protects Our Planet from Tire Waste
Beyond the Barrel: The Versatile Future of Tire Pyrolysis Oil (TPO) Applications
References
[1] Manufacturing of carbon black from spent tyre pyrolysis oil. ScienceDirect. [https://www.sciencedirect.com/science/article/abs/pii/S0959652620333813]
[2] Recycling of waste tire by pyrolysis to recover carbon black. ScienceDirect. [https://www.sciencedirect.com/science/article/pii/S1359836820333953]
[3] Sustainable tire industry: the role of recovered carbon black. Emerton. [https://www.emerton.co/news/evaluating-the-path-to-a-sustainable-tire-industry-unlocking-the-potential-of-recovered-carbon-black]