From Lab to Large Scale: The Journey of Pyrolysis Technology to Global Impact
THE STORIES
TYROIL
6/24/20255 min read
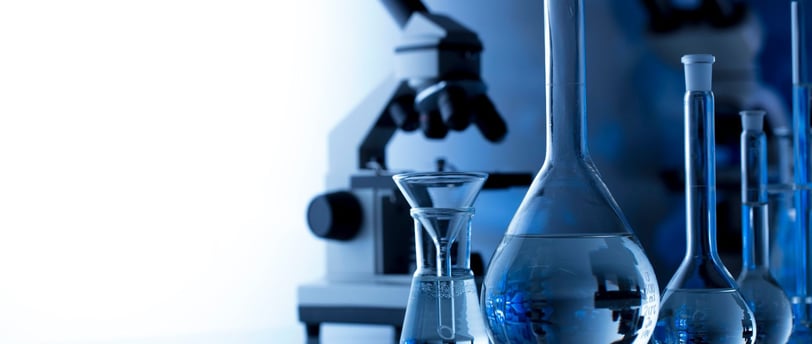
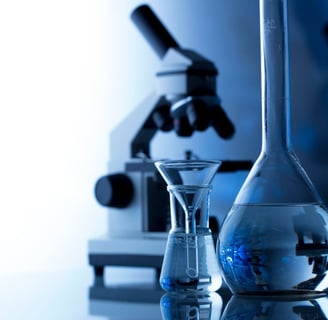
Every groundbreaking innovation begins with a spark – a curious mind, a scientific hypothesis, a small experiment in a quiet laboratory. For tire pyrolysis, that spark ignited decades ago, fueled by the growing global challenge of waste tires. What started as a promising concept in controlled lab settings has embarked on a remarkable journey, overcoming immense engineering and economic hurdles to emerge as a powerful force for sustainability on a global scale. This is the story of how a scientific discovery transitioned from the meticulous precision of the lab to the robust demands of large-scale industrial operation, transforming waste into valuable resources and making a tangible impact worldwide.
The Early Days: A Promising Concept Takes Shape
The idea of breaking down materials through heat in the absence of oxygen, known as pyrolysis, isn't new. Its application to waste tires gained traction as the sheer volume of discarded rubber became an undeniable environmental problem. In the early days, research was primarily conducted in universities and small research facilities. Scientists meticulously studied the optimal temperatures, pressures, and reaction times to convert tires into oil, carbon black, and gas [1]. These initial experiments, often using only a few grams of tire material, proved the technical feasibility of the process. The results were promising: valuable products could indeed be recovered from what was once considered mere waste.
However, the leap from a successful lab experiment to a viable industrial process is monumental. It's like building a miniature model car that runs perfectly, then being asked to design and construct a full-sized, high-performance vehicle capable of transporting thousands of people daily. The challenges were immense, ranging from reactor design and material handling to energy efficiency and product quality consistency.
Scaling Up: Engineering Challenges and Solutions
Scaling up pyrolysis technology meant confronting a new set of engineering complexities. Lab-scale reactors, often small and simple, were inadequate for processing tons of tires per hour. Engineers had to design and build much larger, more robust systems capable of continuous operation. Key challenges included:
Reactor Design: Choosing between batch and continuous reactors, and designing systems that could handle the sticky, abrasive nature of tire materials at high temperatures without fouling or breakdown [2]. Continuous reactors, which allow for a steady feed of material and constant product output, became the preferred choice for large-scale operations due to their higher efficiency and throughput.
Heat Transfer: Ensuring uniform heating of large quantities of tires within the reactor was critical for consistent product quality. Innovative heat exchange mechanisms and reactor configurations were developed to achieve this.
Product Separation and Purification: The raw products from pyrolysis – crude oil, carbon black, and syngas – needed further processing to meet market specifications. This involved designing efficient condensation systems for the oil, separation and grinding systems for the carbon black, and purification systems for the syngas [3].
Emissions Control: While pyrolysis is inherently cleaner than incineration, large-scale plants still require sophisticated emission control systems to ensure compliance with environmental regulations and protect air quality [4].
Overcoming these engineering hurdles required significant investment in research and development, drawing on expertise from chemical engineering, mechanical engineering, and materials science. The result was the development of advanced pyrolysis plants that are not only efficient but also environmentally sound.
Economic Viability and Investment: Attracting the Capital
Beyond technical feasibility, the economic viability of large-scale pyrolysis plants was a critical factor in their journey to global impact. Early plants often struggled with high capital costs, inconsistent product quality, and uncertain market demand for their outputs. However, as technology matured and the value of recovered products became clearer, the economic picture began to change.
Economies of Scale: Larger plants can process more waste tires at a lower cost per ton, improving profitability. This scale also makes it more attractive for investors [5].
Market Development for Products: The growing demand for sustainable materials and fuels has created robust markets for Tire Pyrolysis Oil (TPO) and recovered carbon black (rCB). As industries seek to reduce their carbon footprint and embrace circular economy principles, the value of these products increases [6].
Policy Support and Incentives: Government policies, such as landfill bans, extended producer responsibility schemes, and carbon credits, have significantly improved the economic attractiveness of pyrolysis projects by creating a demand for their services and products [7].
Today, many large-scale pyrolysis projects are proving to be economically viable, attracting significant investment from both private and public sectors. This financial backing is crucial for the continued expansion and global impact of the technology.
Real-World Success Stories: Making a Global Impact
The journey from lab to large scale is punctuated by numerous success stories around the world. Companies and initiatives in various regions have successfully deployed large-scale pyrolysis plants, demonstrating their capacity to address the waste tire challenge and contribute to a circular economy:
Europe: Countries in Europe have been at the forefront of adopting pyrolysis, driven by stringent environmental regulations and a strong commitment to circular economy principles. Large-scale plants are converting millions of tires annually, producing fuels and materials for various industries [8].
Asia: With massive populations and rapidly growing economies, Asian countries are facing immense waste tire challenges. Pyrolysis technology is being increasingly adopted to manage this waste, often with government support and private investment [9].
North America: The US and Canada are seeing a rise in large-scale pyrolysis operations, driven by a combination of environmental concerns, market demand for sustainable products, and technological advancements [10].
These real-world examples are not just isolated incidents; they represent a growing global movement towards sustainable waste management, powered by the successful scaling of tire pyrolysis technology. They demonstrate that what began as a scientific curiosity has evolved into a powerful industrial solution, capable of transforming environmental liabilities into economic assets.
The Future is Scaled: A Testament to Innovation
The journey of tire pyrolysis from a lab curiosity to a global industrial solution is a testament to human ingenuity and perseverance. It highlights the critical interplay between scientific discovery, engineering innovation, economic viability, and supportive policy. As the world continues to grapple with resource scarcity and environmental degradation, the ability to scale up sustainable technologies like pyrolysis will be paramount.
This journey is far from over. With ongoing research, further technological refinements, and continued investment, large-scale tire pyrolysis plants will play an even more significant role in building a truly circular economy, where every old tire finds a new purpose, contributing to a cleaner, more sustainable planet for generations to come.
More Related Articles:
Beyond Compliance: The Future of ESG and Tire Pyrolysis in Corporate Strategy
The Investor's Lens: Why Tire Pyrolysis is Attracting ESG-Focused Capital
The Invisible Shield: How Pyrolysis Protects Our Planet from Tire Waste
What is Tire Pyrolysis Oil (TPO)? Unlocking Energy from Waste Tires
References
[1] Zaki, Z. S. N. R. M., et al. (2025). Global trends of waste tire pyrolysis research. Journal of Cleaner Production, 440, 140800. [https://www.sciencedirect.com/science/article/pii/S2772783125000135]
[2] Afash, H., et al. (2023). Recycling of Tire Waste Using Pyrolysis: An Environmental and Economic Review. Sustainability, 15(19), 14178. [https://www.mdpi.com/2071-1050/15/19/14178]
[3] Zhang, M., et al. (2024). A review on waste tires pyrolysis for energy and material recovery from the optimization perspective. Energy Conversion and Management, 302, 118086. [https://www.sciencedirect.com/science/article/abs/pii/S1364032124002545]
[4] Pivato, A., & Vanin, S. (2024). Air-Polluting Emissions from Pyrolysis Plants: A Systematic Mapping. Sustainability, 11(7), 149. [https://www.mdpi.com/2076-3298/11/7/149]
[5] ScienceDirect. (2022). An economic analysis of scrap tire pyrolysis, potential and new developments. [https://www.sciencedirect.com/science/article/pii/S2405844022029577]
[6] GTSTrading. (2025, February 11). Challenges and Opportunities in Scaling Pyrolysis Technology. [https://gtstrading.vn/2025/02/11/challenges-and-opportunities-in-scaling-pyrolysis-technology/]
[7] ResearchGate. (2024, September 16). Circular economy in Latin America and the Caribbean. [https://research.utwente.nl/files/464074856/1-s20-S235255092400263X-main.pdf]
[8] Zaki, Z. S. N. R. M., et al. (2025). Global trends of waste tire pyrolysis research. Journal of Cleaner Production, 440, 140800. [https://www.sciencedirect.com/science/article/pii/S2772783125000135]
[9] LinkedIn. (2025, May 21). Tyre Pyrolysis Plant Market Future Trends, Challenges, Key Players, and Forecast. [https://www.linkedin.com/pulse/tyre-pyrolysis-plant-market-future-trends-challenges-dygoc]
[10] LinkedIn. (2025, June 13). US Tyre Pyrolysis Plant Market: Unveiling Competitive Dynamics & Growth Opportunities. [https://www.linkedin.com/pulse/us-tyre-pyrolysis-plant-market-unveiling-competitive-dynamics-2nvwc/]